What Essential Documents Should Be Stored in Your MSDS Box for Workplace Safety?
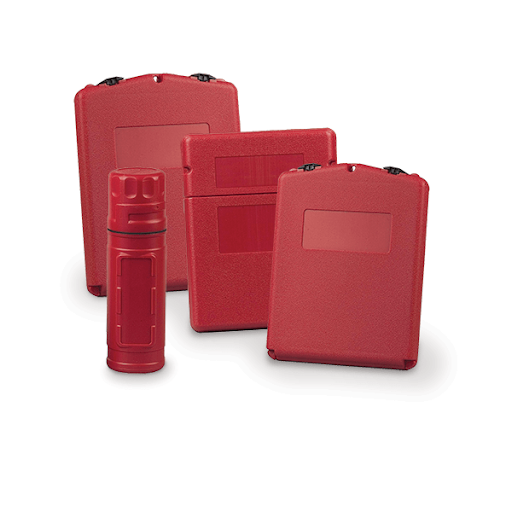
Workplace safety is a paramount concern for employers and employees alike. Beyond mere regulatory compliance, it is a commitment to creating an environment where individuals can perform their tasks without undue risk to their health and well-being. A safe workplace not only protects employees but also enhances productivity and fosters a positive work culture.
In this context, the Material Safety Data Sheet (MSDS) box plays an essential role in maintaining workplace safety. It serves as a centralised repository of critical information related to hazardous materials used in the workplace. It also provides quick access to vital details, ensuring that employees, emergency responders, and management have the necessary information to respond effectively in case of an emergency. Interested? Read on to find out more.
What is MSDS Box?
The MSDS box is a designated and organised storage container within a workplace that holds important documents related to the safety and handling of hazardous materials. The purpose of the MSDS box is to provide quick and easy access to information about the potential hazards, safe use, and emergency procedures associated with chemicals and substances used in the workplace.
Key Elements of an MSDS Box
Having an organised and up-to-date MSDS Box helps ensure that employees, emergency responders, and management have access to the information needed to respond effectively to any hazardous situations that may arise in the workplace. The key contents of an MSDS Box include:
Material Safety Data Sheets (MSDS)
MSDSs provide detailed insights into the composition of materials, potential hazards associated with them, safe handling procedures, and measures to be taken in case of emergencies. By offering a thorough understanding of the properties and risks associated with each substance, MSDSs empower employees to work safely and respond appropriately to any unforeseen situations.
Emergency Contact Information
This segment of the MSDS box is dedicated to ensuring swift and effective responses to emergencies. It includes contact details for external emergency services, allowing for rapid coordination in the event of accidents or hazardous incidents. Additionally, internal contact information for key personnel within the company is provided, streamlining communication and facilitating prompt decision-making during critical situations.
First Aid Procedures
Contained within the MSDS box, first aid procedures are invaluable resources that guide individuals in administering immediate care in the aftermath of accidents or exposure to hazardous materials. These instructions cover essential steps to be taken on-site before professional medical assistance arrives, aiming to minimise the impact of injuries and prioritise the well-being of those involved.
Evacuation Plans
The MSDS box features clear and detailed evacuation plans, including information on designated escape routes and assembly points. These plans are crucial for ensuring a structured and organised evacuation process during emergencies, minimising chaos and promoting the safety of all personnel. By providing clear guidelines, evacuation plans contribute to an efficient response to unforeseen events.
Chemical Inventory
Acting as a comprehensive record-keeping tool, the chemical inventory section of the MSDS box lists all chemicals present in the workplace. This includes essential details such as quantities and specific storage locations. This information not only aids in the day-to-day safe handling of materials but is also critical for emergency response planning. Having an accurate and up-to-date chemical inventory enhances overall workplace safety by providing a comprehensive overview of the substances in use.
Tips for Organising the MSDS Box for Easy Access
Categorisation
Group MSDS documents by categories such as chemical type, department, or usage to facilitate quicker retrieval. Consider using color-coded tabs or folders for easy visual identification.
Alphabetical Order
Arrange MSDS documents alphabetically by the name of the chemical or product, streamlining the search process.
Update Regularly
Ensure that all MSDS documents are current and up-to-date. Also, establish a regular schedule for reviewing and updating information and removing outdated documents promptly.
Clearly Labelled Sections
Use clear labels for each section within the MSDS box, such as “Chemical A-Z,” “Emergency Contacts,” and “Evacuation Plans.”
Emergency Procedures at the Front
Place emergency procedures, contact information, and evacuation plans at the front of the MSDS box for immediate access during crises.
Employee-Friendly Layout
Consider the usability of the MSDS box for employees, arranging documents in a logical order that aligns with how they may search for information.
Accessible Location
Keep the MSDS box in a central and easily accessible location within the workplace. Ensure it is well-lit and clearly marked to guide individuals to its location quickly.
Digital Back-Up
Consider maintaining a digital copy of MSDS documents, ensuring redundancy and providing an additional means of access.
Importance of Training Employees on MSDS Box Location and Use
Training employees on the MSDS box’s location and use is the compass that guides swift and informed responses, transforming information into action and fostering a culture where safety is not just a priority but a shared responsibility. Here’s why:
- It ensures a swift response in emergencies. Familiarity with its whereabouts allows for immediate access to critical information.
- Well-trained employees understand how to use the information in the MSDS box effectively, enabling them to make informed decisions during hazardous situations.
- Knowing the location and contents of the MSDS box minimises the time it takes for employees to access important details, contributing to a faster and more efficient response to emergencies.
- Employee training on the MSDS box aligns with regulatory requirements for workplace safety, demonstrating the company’s commitment to compliance.
- By educating employees on the importance of the MSDS box and its contents, a culture of safety is fostered within the workplace, promoting proactive hazard awareness and prevention.
- Training instils confidence in employees, empowering them to respond effectively to unforeseen events and contribute to maintaining a safe work environment.
By combining an organised MSDS box with thorough employee training, a company can create a robust system that not only complies with safety regulations but also actively promotes a culture of safety and preparedness among its workforce.
Related: WHAT IS HAZMAT MANIFEST BOX
A Secure Tomorrow Begins Today!
Ensuring the accessibility of important papers while shielding them from the elements is paramount, and Ecospill offers a comprehensive solution. Whether it’s the sturdy and reliable MSDS Document Storage Box or the robust Hazchem Emergency Information Cabinet, both options stand as sentinels against moisture and dirt. With Ecospill’s offerings, you not only secure MSDS sheets but also keep equipment manuals and emergency information at your fingertips, ready for immediate use. For the ultimate safeguard in workplace documentation, explore our range today and start your journey towards a safer, more secure tomorrow.